Полипропиленовых волокон TREVON
ТЕХНОЛОГИИ
Полипропиленовое штапельное волокно можно производить классическим двухступенчатым процессом или одноступенчатым компактным формованием.
Технологическое оборудование
Фирма TREVOS Košťálov s.r.o. использует для производства полипропиленового штапельного волокна одноступенчатое оборудование непрерывного действия от известной немецкой фирмы Fleissner GmbH & Co.(субпоставщиком формующих нитеобразователей является фирма Rieter GmbH упаковочных прессов фирма AUTEFA GmbH).
Одноступенчатый процесс, в отличие от двухступенчатого, применяется при производстве волокон на линиях с малым объемом продукции (порядка тысяч тонн в год) и отличается скоростями формирования, примерно в 10 – 20 раз меньшими, чем при процессе обычном.
Одноступенчатый процесс, однако, менее требовательный с экономической точки зрения (первоначальная стоимость и эксплуатационные расходы), занимает меньше места, технологическое оборудование более низкое и одновременно, примерно в 10 раз более гибкое при изменении производственной партии (экономически приемлемая партия у этого процесса равна нескольким тоннам и изменение выпускаемого вида продукции осуществляется в течение нескольких часов).
Технологический процесс

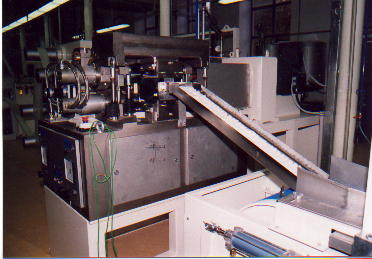
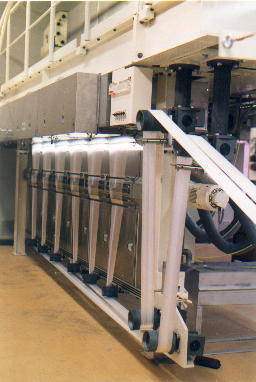

Гранулированый полипропилен автоматически дозируется в червячный экструдер, в котором полипропилен при определенной температуре расплавится и гомогенизируется. Потом расплав подается по трубопроводу на формующее устройство, где продавливается формующими насосами через фильеры. Формующее устройство может содержать несколько блоков фильер, в каждом может быть несколько десятков тысяч фильер.
Волокна оттягиваются от форсунок с определенной скоростью, решающей для линейной массы (тонкость) волокон. С помощью приводимого в движение смачивающего валка на них наносится авиваж (целью которого является улучшение последующей переработки волокон уменьшением электризации, ограничением сцепляемости нитей, улучшением поверхности…). И потом отдельные нити сводятся в жилы, которые потом сводятся в один или более жгутов (кабелей).
Оттягивание волокон обеспечивается так называемым первым тянущим (или протягивающим) механизмом, в котором жгут волокон, проходит через систему, состоящую, как правило, из 7 горизонтальных валков, т.н. галет.
В секции между первым и вторым протягивающим механизмом волоконный жгут необходимо удлинить, это значит, что наиболее сориентировать молекулярные цепи полимера в направлении оси вытягивания и, в результате этого придать волокнам необходимые механические свойства. Это осуществляется движением галет второго протягивающего механизма со скоростью в несколько раз большей, чем галет первого механизма.
В пространстве между обоими механизмами, кроме этого, жила проходит через паровыпускное окно, где на волокно воздействует высокая температура, обеспечивающая осуществление вытягивающего процесса.
После соответствующего удлинения волокон, жгут волокон направляется в гофрировочный механизм (crimper), в котором отжимается из волокон избыточная авиваж, но, прежде всего в которых вдавливанием жгута в камеру для придания извитости происходит его гофрировка.
Последней частью процесса, решающей для свойств волокон, является термофиксация, предотвращающая нежелательные изменения (под воздействием напряжения в волокнах в результате охлаждения) уже достигнутых параметров.
В заключение потом жила волокон нарезается на отдельные волокна установленной длины в режущей машине и потом транспортируется уже готовое штапельное волокно в пресс, в котором происходит его сжатие в форму пакета данных размеров и массы.