Polypropylene Fibres TREVON
PROCESS TECHNOLOGY
Polypropylene staple fibers can be produced by two different variants of the melt spinning process - by the conventional 2-stage process or by the single-stage compact spinning process.
Production facilities
The company TREVOS Kostalov s.r.o. uses for the production of polypropylene staple fibers two single-stage compact spinning lines made by renowned German company Fleissner(the supplier of spinning units are the companies Rieter and SRK Engineering and the subcontractor of the baling presses is the firmAUTEFA).
The single-stage process is employed for the production of fibers on small throughput lines (several thousand tons/year) and the spinning speeds are then very low (10-20 times lower).
The single-stage process is becoming more important in economic terms. It is distinguished by low machine heights and it is much more flexibel in terms of minimal batch size than the 2-stage process is (economically acceptable batch is few tons, a product change is possible within shortest time of 1 hour).
Process Technology

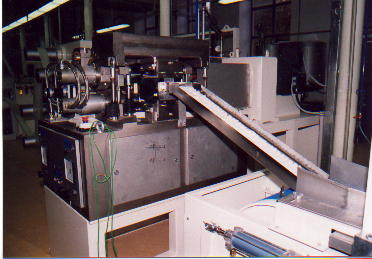

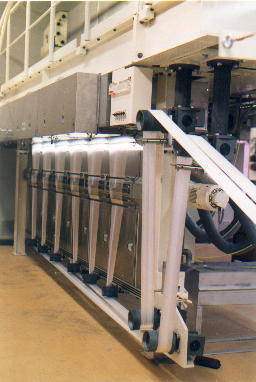
First, polypropylene granulate is dosed into the extruder, where it is molten, uniformly tempered and homogenized. The melt is then fed by spinning pumps through the spinnerets built in the spinning beam. In the spinning beam can be placed couple of spinneret packs having many thousand of nozzle bores.
Filaments are taken down from the spinnerets at a speed given. This speed is decisive as for the fineness of fibers. After the cooling, the spin finish application is effected by a driven kiss-roll system. The spin finish should improve the processabillity - due to the decrease of electrostatic charging and friction, improve the touch . Particular filaments are lead together into the bundles and these bundles are combined into the one or several spinning tows.
The drawing-off is realized by the first drawstand, where the tow passes over a system of 7 cylinders, so called godets. The tow has to be subjected to the drawing between the first and the second drawstand. It means that the macromolecule chains of polypropylene must be as oriented in the direction of drawing as possible to reach the required machanical properties. Therefore, the speed of the second drawstand godets have to be higher (drawing ratio up to approx. 5) than the speed of the first ones.
In the space between the both drawstands is the tow heated up by application of steam.
After the fibers have been stretched enough, the tow is directed into the crimper. The lubricant is pressed away here and the tow is textured in the stuffer box to give fibers the textile properties.
The final stage decisive in terms of mechanical properties of fibers is heat setting (drying), that prevents the undesirable changes of properties (sudden relax of tensile stresses by cooling). At the end is the tow cut into many staple fibers of defined length. Then follows the transport of the cut fibers into the baling press and the fibers get the form of bales.