Polypropylenfaser TREVON
TECHNOLOGIE
Polypropylenfasern können im klassischen Zweistufenprozess oder durch einstufige kompakte Verfaserung hergestellt werden.
Produktionseinrichtungen
Die Firma TREVOS Košťálov s.r.o. nutzt zur Herstellung von Polypropylenfasern einstufige kontinuierliche Einrichtungen der renommierten deutschen Firma Fleissner GmbH & Co. (Sublieferant der Fasereinheiten ist die Firma Rieter GmbH und der Verpackungspressen die Firma AUTEFA GmbH).
Der Einstufenprozess wird im Unterschied zu dem zweistufigen bei der Herstellung von Fasern auf Produktionslinien mit einer niedrigeren Produktion (reihenweise in tausend Tonnen jährlich) zur Geltung gebracht und zeichnet sich mit einer ca. 10-20malig geringeren Geschwindigkeit der Verfaserung als bei konventionellen Methode aus.
Der Einstufenprozess ist allerdings aus ökonomischer Sicht weniger anspruchsvoll (Anschaffungs- und Betriebskosten), hat geringere Ansprüche an den Platz, kleinere Maschineneinrichtungen und gleichzeitig ca. 10mal flexibler soweit es um die Änderung der Produktionscharge (eine ökonomisch annehmbare Charge beträgt bei diesem Prozess einige wenige Tonnen und eine Änderung des hergestellten Typs in reihen von Stunden) geht.
Prozesstechnologie

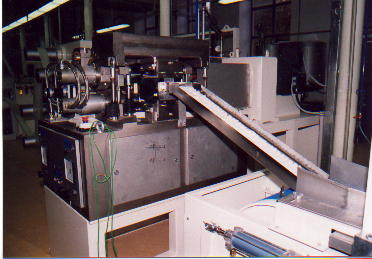

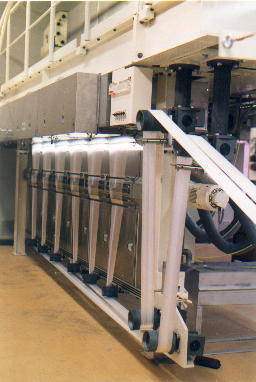
Polypropylengranulat wird automatisch in den Schneckenextruder dosiert, wo das Polypropylen in einer bestimmten Temperatur geschmolzen und homogenisiert wird. Das Schmelzgut wird danach durch Rohrleitungen zum Faserbalken transportiert, wo dieses mit Hilfe von Verfaserungspumen durch Düsen gedrückt wird. Der Faserbalken kann mehrere Düsenblöcke enthalten, wobei in jedem bis zu mehreren zehntausend Düsen sein können.
Die Fasern werden mit einer bestimmten Geschwindigkeit von den Düsen abgezogen, welche für das Längengewicht (Feinheit) der Fasern entscheidend ist, mit Hilfe einer angetriebenen Befeuchtungswalze wird auf diese Avivage aufgetragen (welche die Verbesserung der nachfolgenden Verarbeitung der Fasern durch Verringerung der elektrostatischen Aufladung, Einschränkung des Zusammenhalten der Filamente, eine Oberflächenveredelung als Aufgabe hat) und nachfolgend werden die einzelnen Filamente in die Litzen geführt und diese danach in einen oder mehrere Verbünde (Kabel)
Der Abzug der Fasern wird durch das sogen. erste Abzug- (oder Durchzug-) Werkzeug gesichert, wo der Fasernverbund ein, in der Regel ein System von 7 horizontalen Walzen, sogen. Galetten durchläuft.
In dem Teilstück zwischen dem ersten und zweiten Durchzugswerkzeug ist es nötig den Faserverbund zu verlängern, d.h. die Molekularkette der Polymere so weit wie möglich in der Verlängerungsachse auszurichten und den Fasern damit die benötigte mechanische Eigenschaft zu geben. Dies wird dadurch realisiert, dass die Gallete des zweiten Durchzugswerkzeuges sich mit einer mehrfach höheren Geschwindigkeit bewegt als das des ersten Werkzeuges.
Im Bereich zwischen den beiden Maschinen durchlaufen die Litzen des weiteren einen Dampfkanal, wo auf die Fasern eine hohe Temperatur einwirkt, welche den Verlängerungsprozess ermöglicht.
Nach der entsprechenden Faserverlängerung richten sich die Fasern in eine Staucheinrichtung (crimper), wo die überflüssige Avivage aus den Fasern gedrückt wird, aber wo vor allem durch das Drücken der Fasern in die Stauchkammer deren Kräuselung erzielt wird.
Der letzte Prozessteil, entscheidend über die Eigenschaften der Fasern ist die Wärmefixierung, welche ungewollten Veränderungen (unter dem Einfluss der Spannungsbefreiung der fasern bei der Abkühlung) der bereits erzielten Eigenschaften verhindert.
Zum Abschluss wird danach die Faserlitze in der Schnittmaschine auf einzelne Faser einer festgelegten Länge geschnitten und es folgt der Transport der fertigen Garne in die Presse, wo die Kompaktierung in Paketform gegebener Ausmaße und Gewichte erfolgt.